Lifteurop on their tool to monitor lifting systems
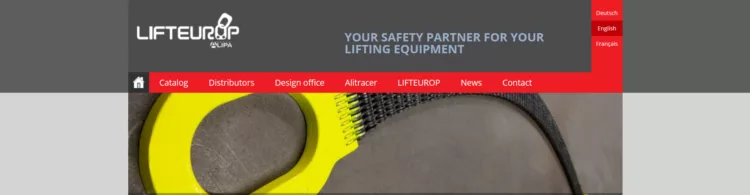
We spoke with Christophe Losange, Director of Lifteurop, a Luxembourgish company that specializes in lifting equipment and accessories. He told us about their Alitracer application, a traceability management tool for lifting.
Lifteurop designs, manufactures and distributes standard or specific lifting equipment and accessories. Today, the company is an international benchmark in the production and distribution of lifting accessories for aeronautics, the automotive industry and automotive components, the shipbuilding industry, the steel industry, heavy industry, administration and army.
The success of Lifteurop is due to a team of 10 passionate employees working in sales, customer service, purchases, technical or production department.
Christophe Losange, the brand’s Director, is one of the oldest employees. Born in Belgium, Christophe initially joined the Alipa Group as Technical and Sales Manager, before becoming a member of management in April 2004. He introduced us to the company's flagship tool, the Alitracer application, a tool specialised in traceability management for lifting.
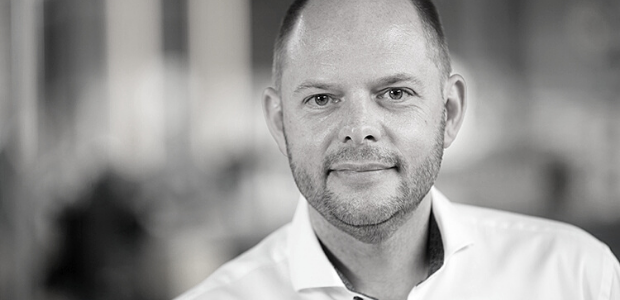
Christophe Losange, Director of LIFTEUROP
Simplifying control procedures
Alitracer was created to meet the demands of Lifteurop customers, who were looking for a solution to improve the management of accessories and lifting systems, and any other equipment that needs to be regularly checked, such as forklifts, overhead cranes, etc. Lifting accessories must undergo an annual check which can be tedious, especially if the operating sites are numerous.
Most lifting companies manage their equipment with an Excel spreadsheet, while the safety body approved for lifting companies uses a different interface. For this reason, Lifteurop sought a solution that would centralize all information and be suitable for both the companies and the organization.
Alitracer is a modern tool that provides access to a complete inventory of all lifting systems and to all useful information: whether it is the last place where the products were scanned, their wear status or even the management of security checks, thanks to a direct access to the maintenance log and automatically scheduled annual checks.
The application allows real-time monitoring of the control status of lifting systems, enhancing safety and ensuring safe usage in accordance with legislation.
Safety as a fundamental brand value
The original idea of this tool was to protect users from the dangers of using faulty slings:
“We started from the premise that no serious business leader wants to play with the safety of their employees. However, the reality is not always that simple. In practice, when you have sites all over the country, it is not easy to know what equipment you have, where it is and in what condition it is. Today, everyone is handling this issue in their own way, as a good father. There are solutions, but they require investment in expensive equipment. Our idea was to offer an efficient tool at an affordable price ", explains Christophe Losange
Digitalisation as a goal
Before the application was created, the periodic checks were a completely manual operation. This legal obligation requires that each accessory be provided with a CE marking as well as instructions. These documents were previously stored in a filing cabinet.
With Alitracer, an Internet connection is sufficient to view the status and history and all of these documents are accessible through the application. Its greatness is that it allows the user to monitor the inspection status of the lifting equipment and accessories and to be informed of real time status changes. It offers centralized access to all information about your equipment and ensures compliance with legislation by automatically scheduling mandatory annual checks.
The periodic check no longer requires manual note taking. All you have to do at the end of the day is use the application to view the machines that have been checked and the associated comments. It is also possible to export or import data and build reports. Thanks to an integrated chip, it is possible to scan the QR code of lifting systems, to place your smartphone on the NFC chip or to register manually to find the usage status:
• green (safe to use)
• orange (caution, control is necessary)
• red (defective accessory or equipment)
The application is designed for 3 levels of users with access to different functions depending on their status: the operator, the controller and the fleet manager.
Where is the app available?
The Alitracer app is available in several languages and can be downloaded on iPhone or Android. It can be used for all lifting equipment and accessories, whatever the brand or the supplier. For Lifteurop accessories and lifting equipment, the chips are included and the information pre-encoded.
Lifteurop is a lifting company based in Luxembourg. Christophe Losange shared his entrepreneurial story with EuroDNS as part of the #WeSupportBrands campaign. Are you a EuroDNS customer? Find out how to share your own business story.
5 Stunning WordPress Homepages to Boost Conversions
22 Profitable Online Business Ideas for 2021
Related articles: